Unlocking the Potential of Plastic Injection Moulding
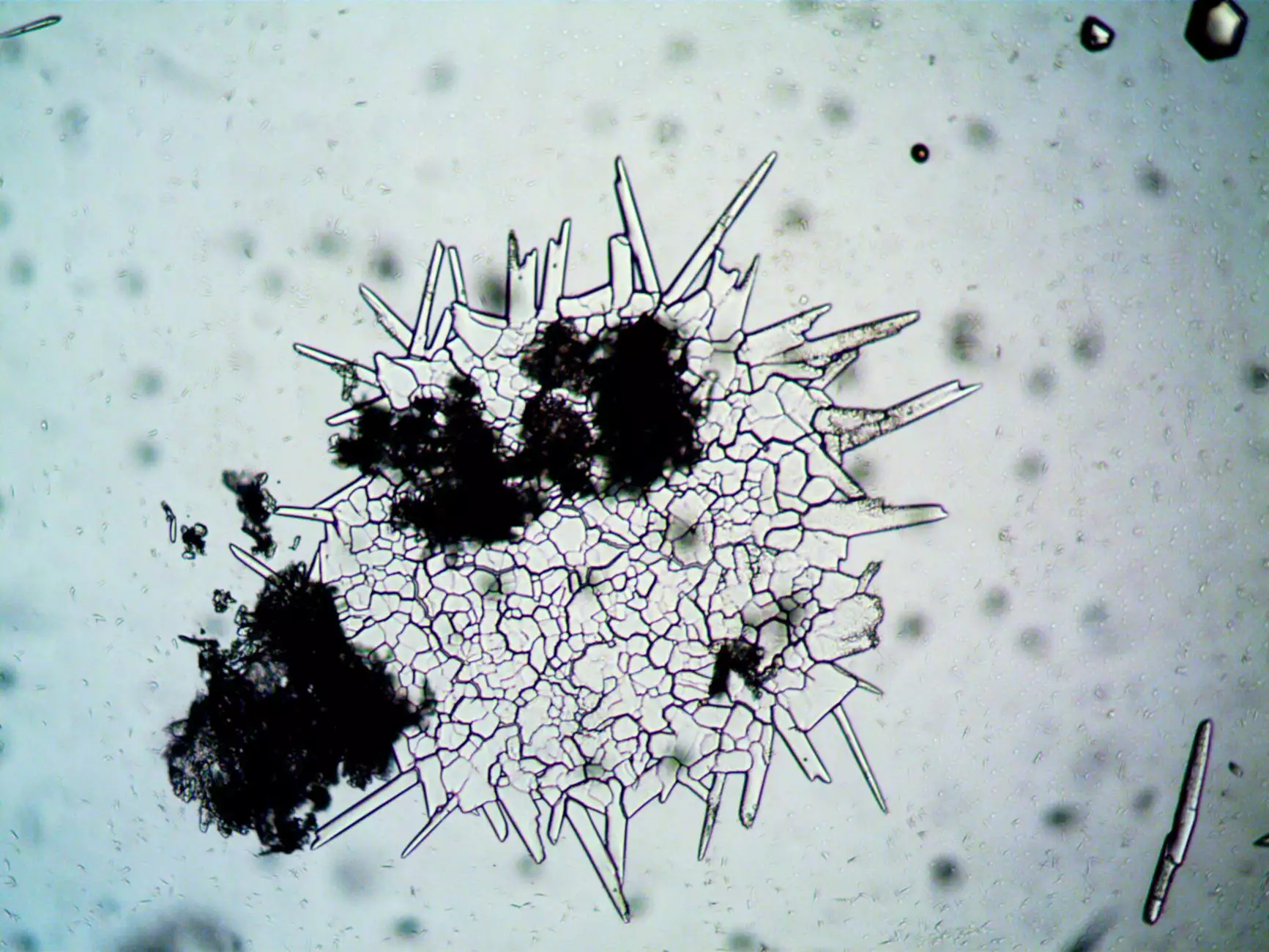
Plastic injection moulding stands as one of the most versatile and widely utilized manufacturing processes in the modern industry. Whether producing everyday items or complex components, the process is critical to the efficiency and precision required in today’s competitive market.
Understanding Plastic Injection Moulding
At its core, plastic injection moulding is a manufacturing method for producing parts by injecting molten material into a mould. It is essential for creating intricate shapes and is commonly used in producing plastic parts for various industries including automotive, medical, aerospace, and consumer goods.
How Does Plastic Injection Moulding Work?
The plastic injection moulding process generally involves the following steps:
- Design the Part: Before anything else, it is crucial to design the component that will be produced. This involves 3D modelling to ensure precision.
- Making the Mould: A mould is crafted, usually from steel or aluminum, based on the specifications of the part design. This tool is essential for shaping the plastic material.
- Injection: Once the mould is ready, plastic pellets are fed into the injection machine where they are heated until they melt. The molten plastic is then injected into the mould under high pressure.
- Cooling and Solidification: The plastic within the mould is cooled to solidify into the desired shape.
- Finishing: After cooling, the mould is opened, and the newly formed part is ejected. Additional finishing processes may be required to enhance the product.
Key Advantages of Plastic Injection Moulding
When done correctly, plastic injection moulding offers numerous benefits that can significantly impact a business's production capabilities:
- High Efficiency: The process is highly efficient, allowing for rapid production rates that save time and reduce labor costs.
- Design Flexibility: Complex geometries and detailed designs can be produced easily, making it ideal for a variety of applications.
- Minimal Waste: Since material usage is optimized during the process, scrap and waste are minimal compared to traditional machining.
- Consistency and Quality: The process allows for consistent replication of parts with high precision, ensuring uniform quality across production batches.
- Material Variety: A wide range of plastics and blends can be utilized, enabling businesses to choose materials that meet their specific requirements.
The Applications of Plastic Injection Moulding
The versatility of plastic injection moulding extends across numerous sectors. Here’s a closer look at some key industries where this process shines:
1. Automotive Industry
Within the automotive sector, manufacturers utilize plastic injection moulding to create myriad components including dashboards, panels, and other interior and exterior parts that require durability and precision.
2. Medical Device Manufacturing
Healthcare relies on plastic injection moulding for creating surgical instruments, disposable syringes, and other vital components, ensuring compliance with stringent hygiene standards and performance requirements.
3. Consumer Goods Production
Everyday items such as containers, toys, and household products often originate from plastic injection moulding, allowing for mass production at lower costs while ensuring quality.
4. Electronics
The electronics industry benefits from plastic injection moulding in producing casings, connectors, and various internal components, emphasizing the need for both aesthetic appeal and functionality.
Types of Moulding Processes
There are several types of plastic injection moulding processes, each tailored to specific applications:
- Thermoplastic Injection Moulding: Involves thermoplastics that can be remelted. It’s widely used for creating durable products.
- Thermoset Injection Moulding: Utilizes thermosetting plastics that harden once cured, suitable for durable and heat-resistant parts.
- Gas-assisted Injection Moulding: Incorporates gas to create hollow sections within the part, reducing weight and material usage.
- Multi-material Injection Moulding: Allows for the injection of two or more materials simultaneously, ideal for creating complex assemblies.
Choosing the Right Partner for Your Plastic Injection Moulding Needs
When considering plastic injection moulding, choosing the right manufacturing partner is crucial. Here are key aspects to evaluate:
1. Experience and Expertise
Look for a partner with substantial experience in plastic injection moulding. An expert team can navigate complex design challenges and ensure high-quality outcomes.
2. Technological Capabilities
Ensure that the partner employs modern machinery and technologies, such as CAD/CAM solutions for design and simulation, which enhances accuracy and efficiency.
3. Quality Assurance Procedures
Quality control is vital in maintaining standards. Verify that the partner has a robust QA system in place to monitor production processes and enforce quality checks.
4. Customization Options
The ability to provide customized solutions is a major advantage. A flexible partner can adapt to your specific requirements, whether in design, materials, or production volume.
Future Trends in Plastic Injection Moulding
The landscape of plastic injection moulding is continuously evolving. Here are some trends shaping its future:
1. Automation and Smart Manufacturing
The integration of automation and robotics in the injection moulding process is increasing, enhancing efficiency and reducing production times.
2. Sustainability Efforts
With a growing focus on environmental impacts, many manufacturers are exploring biodegradable materials and recycling technologies to reduce waste and promote sustainability.
3. Advanced Material Technologies
Innovations in material science are leading to the development of new plastics that offer improved performance characteristics, such as higher strength and thermal stability.
4. Custom Software Solutions
Custom software for estimating costs, managing production schedules, and optimizing workflow is gaining traction among plastic injection moulding companies.
Conclusion
In a world that demands high efficiency, precision, and adaptability, plastic injection moulding emerges as a cornerstone of modern manufacturing. Businesses seeking to leverage this technology can greatly benefit by understanding its intricacies, advantages, and applications.
As seen on deepmould.net, partnering with experienced moulding experts can lead to unparalleled product quality and innovation. By harnessing the power of plastic injection moulding, companies can position themselves at the forefront of their industries, meeting consumer demands and driving growth.