Custom CNC Machining Parts: Revolutionizing Metal Fabrication
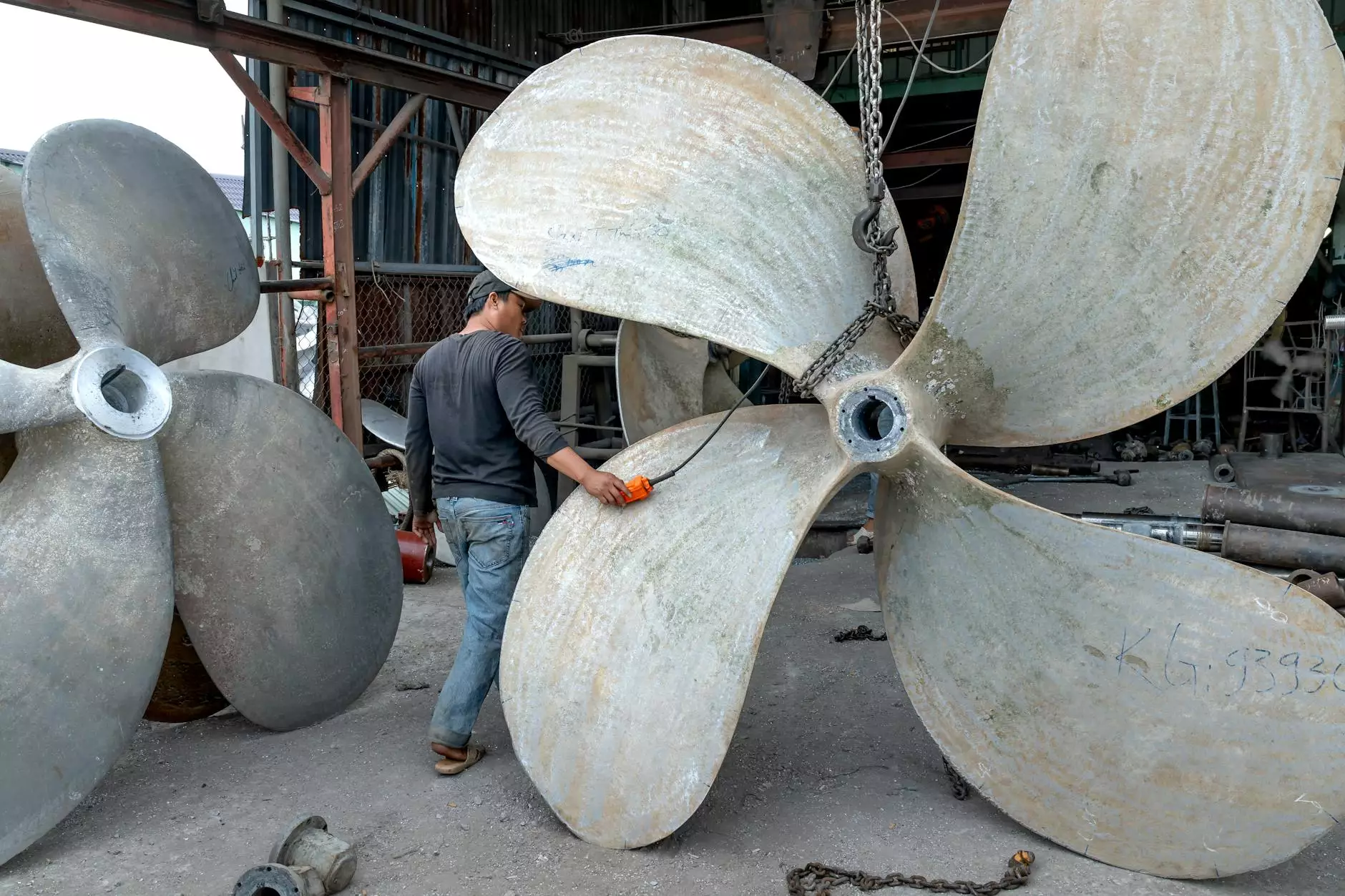
Custom CNC machining parts have emerged as a cornerstone of modern metal fabrication, providing businesses with unparalleled precision, versatility, and efficiency. As industries across the globe continue to evolve, the demand for bespoke solutions tailored to specific needs has never been higher. This article delves into the numerous benefits, processes, and applications of custom CNC machining, showcasing how it can propel your business to new heights and ultimately enhance productivity and profitability.
Understanding CNC Machining
CNC, or Computer Numerical Control, machining refers to the automated control of machining tools through a computer. This technology allows for the transformation of raw materials into finished products with a degree of accuracy that manual machining simply can't match. CNC machining is not only used for machining parts but also incorporates a range of manufacturing processes, including turning, milling, drilling, and electro-discharge machining (EDM).
The Benefits of Custom CNC Machining Parts
Investing in custom CNC machining parts offers a multitude of benefits that can positively influence your manufacturing capabilities:
- Precision Engineering: CNC machines operate with incredible accuracy, ensuring that every component meets the specified tolerances and dimensions.
- Repeatability: Once a program is set, CNC machines can produce thousands of identical parts with the same precision, drastically reducing human error.
- Material Flexibility: CNC machining can work with various materials, including metals, plastics, and composites, making it suitable for diverse applications.
- Complex Designs: Complex geometries that are often impossible to achieve with traditional methods can be manufactured with ease using CNC technology.
- Cost Efficiency: While the initial setup costs may be higher, the long-term savings associated with reduced waste and increased production rates lead to favorable ROI.
Applications of Custom CNC Machining Parts
Custom CNC machining parts serve a wide array of industries, highlighting their versatility and importance:
Aerospace Industry
The aerospace sector demands the highest levels of precision and reliability. Custom CNC machining parts are integral in manufacturing components such as:
- Engine casings
- Landing gear parts
- Structural components
Automotive Industry
CNC machining plays a critical role in the automotive sector, providing parts that enhance vehicle performance and safety. Common applications include:
- Engine blocks
- Transmission components
- Suspension parts
Medical Devices
In the medical field, precision is crucial. Custom CNC machining is used to create:
- Prosthetic devices
- Surgical instruments
- Medical implants
Consumer Electronics
The electronics industry requires intricate parts with high levels of detail. Examples include:
- Circuit board enclosures
- Component housings
- Heat sinks
The Custom CNC Machining Process
1. Design & Prototyping
The journey begins with the design phase. Utilizing CAD (Computer-Aided Design) software, engineers create a detailed blueprint of the desired part. Prototyping is often employed to verify the design’s functionality and feasibility before moving to production.
2. Material Selection
Choosing the right material is crucial, as it affects the part's performance and durability. Common materials used in CNC machining include:
- Aluminum
- Stainless Steel
- Titanium
- Plastics
3. Machining Process
Once the design is finalized and materials are selected, the machining process commences. Depending on the complexity of the component, various techniques may be employed. Common machining operations include:
- Milling: Removes material using rotary cutters.
- Turning: Material is rotated while a cutting tool shapes it.
- Drilling: Creates holes in the material using drill bits.
- EDM: Uses electrical discharges to remove material from a workpiece.
4. Quality Control
To ensure that the output meets the high standards required across industries, rigorous quality control measures are put in place. This often includes:
- Dimensional inspections
- Surface finish evaluation
- Tensile strength testing
Choosing the Right Partner for Custom CNC Machining Parts
Selecting a reliable partner for custom CNC machining parts is paramount for ensuring the success of your projects. Here are key factors to consider:
- Experience: Look for a provider that has a proven track record in the industry and understands the specific needs of your sector.
- Technology: Ensure the company utilizes state-of-the-art CNC machinery and software to deliver high-quality results swiftly.
- Quality Certifications: A company that is certified in quality standards (e.g., ISO 9001) will inherently maintain higher quality levels.
- Customer Support: Opt for a machining partner that offers accessible customer support, open communication, and the ability to adapt to your needs.
The Future of Custom CNC Machining
As technology continues to advance, the custom CNC machining landscape will inevitably evolve. Innovations such as 3D printing, artificial intelligence, and advanced robotics promise to enhance the capabilities of CNC machining. Companies that embrace these advancements will be well-positioned to meet the ever-growing demands of the marketplace.
Conclusion
In an era where precision and customization are paramount, investing in custom CNC machining parts is not merely a worthwhile endeavor but a necessity for businesses looking to thrive. By understanding the benefits, applications, and processes of CNC machining, companies can harness this powerful technology to elevate their production capabilities and, ultimately, their bottom line. As a leader in metal fabrication, DeepMould is poised to assist businesses in realizing their manufacturing goals through expertly crafted custom machining solutions.