Understanding Lathe Turning Parts Manufacturers
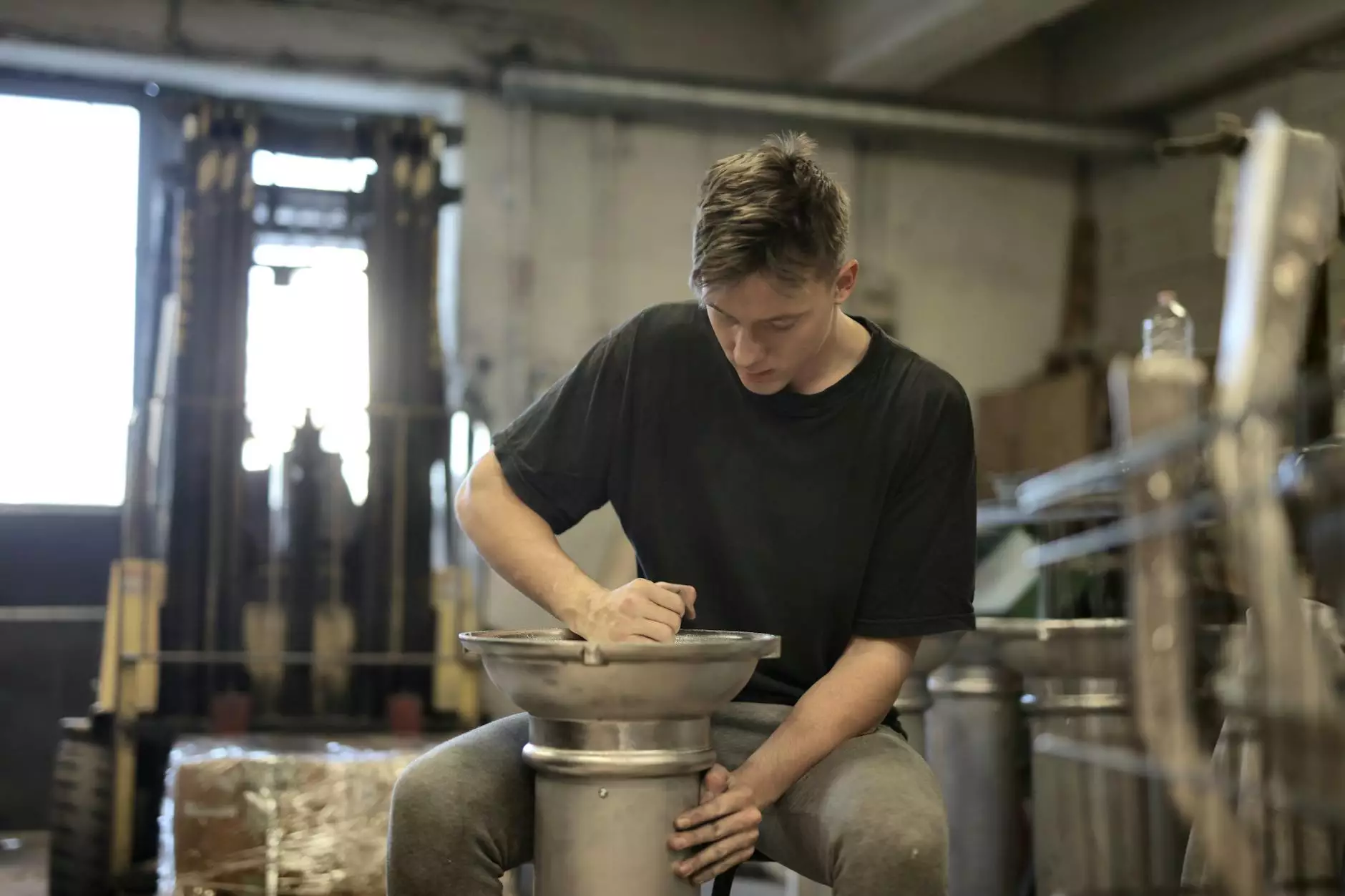
In the realm of precision engineering, one cannot overlook the substantial contribution made by lathe turning parts manufacturers. These manufacturers are pivotal in producing high-quality components that meet the rigorous demands of various industries. In this article, we will delve deep into the intricacies of lathe turning, the benefits it brings, and how selecting the right manufacturer can elevate your business operations.
What is Lathe Turning?
Lathe turning is a machining process where material is removed from a workpiece to create a specific shape or finish. By applying various tools, manufacturers can produce intricate designs that revolve around a central axis. The process is widely appreciated for its accuracy and effectiveness in developing components used across diverse sectors.
Why Choose Lathe Turning Parts Manufacturers?
Selecting a proficient lathe turning parts manufacturer offers numerous benefits:
- Precision and Accuracy: Manufacturers employ advanced machinery and techniques to ensure high precision.
- Customization: Tailored solutions can be crafted to meet specific project requirements.
- Material Versatility: From metals to plastics, a wide array of materials can be used.
- Scalability: Manufacturers can handle both small and large-scale production runs efficiently.
- Cost-Effectiveness: By optimizing processes, manufacturers help reduce operational costs.
Industries Benefiting from Lathe Turning Parts
The components produced by lathe turning parts manufacturers find applications in various industries, including:
- Aerospace: Components for aircraft, including fasteners and valves.
- Automotive: Parts for engines, gearboxes, and other critical systems.
- Medical: Surgical instruments and medical devices requiring high precision.
- Electronics: Enclosures and fixings for electronic devices.
- Construction: Hardware and fixtures used in building and infrastructure.
The Importance of Material Selection
The choice of material is fundamental in the lathe turning process. Different applications demand specific material properties, and the best lathe turning parts manufacturers offer a variety of options. Common materials include:
- Aluminum: Lightweight and resistant to corrosion, ideal for aerospace and automotive parts.
- Steel: Extremely durable, often used in heavy machinery components.
- Copper: Excellent electrical conductivity makes it suitable for electronic applications.
- Plastic: Used for non-metal components, offering flexibility and reduced weight.
Key Processes in Lathe Turning
Understanding the key processes involved in lathe turning helps in appreciating the craftsmanship behind the products:
1. Preparing the Machine
This initial step involves setting up the lathe, selecting the right tool bits, and ensuring that the machine is calibrated for the material being processed. Proper preparation ensures precision in the final product.
2. Workpiece Setup
The raw material is securely mounted on the lathe. The setup can vary depending on whether it's a vertical or horizontal lathe.
3. Turning Process Execution
The machine operates as the cutting tools remove material to achieve the desired shape. Factors like speed, feed rate, and depth of cut are adjusted throughout the process to ensure optimal results.
4. Finishing Techniques
After shaping, finishing techniques such as grinding or polishing may be employed to enhance the component's surface finish, which is crucial for aesthetic and functional purposes.
Quality Control in Lathe Turning
High-quality products stem from rigorous quality control processes overseen by reputable lathe turning parts manufacturers. These processes typically include:
- Dimensional Inspection: Ensures that parts meet specified dimensions.
- Surface Roughness Testing: Assesses the smoothness of the finished product.
- Tensile Testing: Evaluates the strength and ductility of materials used.
- Functional Testing: Confirms that parts operate as intended in real-life applications.
Choosing the Right Lathe Turning Parts Manufacturer
With numerous manufacturers available, selecting the right one is paramount. Here’s how to navigate the selection:
1. Research Their Experience
Look for manufacturers with a proven track record in lathe turning, especially within your industry.
2. Evaluate Their Technology
Ensure they utilize advanced lathes and tools, along with the latest technology to stay competitive.
3. Examine Their Quality Certifications
Certifications like ISO 9001 indicate adherence to international quality standards.
4. Customer Reviews and Testimonials
Genuine feedback from previous clients can provide insights into the manufacturer’s capabilities and reliability.
5. Request Samples
Before placing a large order, request samples to verify their output quality and precision.
Future Trends in Lathe Turning Manufacturing
The landscape of lathe turning manufacturing is evolving rapidly, driven by technology and industry demands. Key trends include:
- Automation: Increased use of CNC lathes for faster, more precise production.
- 3D Printing Integration: Hybrid solutions where traditional machining meets additive manufacturing.
- Smart Manufacturing: IoT-enabled machines for real-time monitoring and optimization.
- Sustainability: Emphasis on eco-friendly materials and waste reduction practices.
Conclusion
In conclusion, lathe turning parts manufacturers are integral to the production of high-quality, precision parts across multiple industries. By understanding this process and selecting the right manufacturer, businesses can ensure they receive components that meet their stringent requirements, paving the way for success in their respective fields. Explore the possibilities that come with quality lathe turning and ensure your business stays ahead in this competitive market. For those looking for a reliable partner in this field, consider the expertise of Deep Mould. With a commitment to excellence in metal fabrication, they can meet all your lathe turning needs.